Choosing the Best Attachments for Your Excavator
- Construction Management
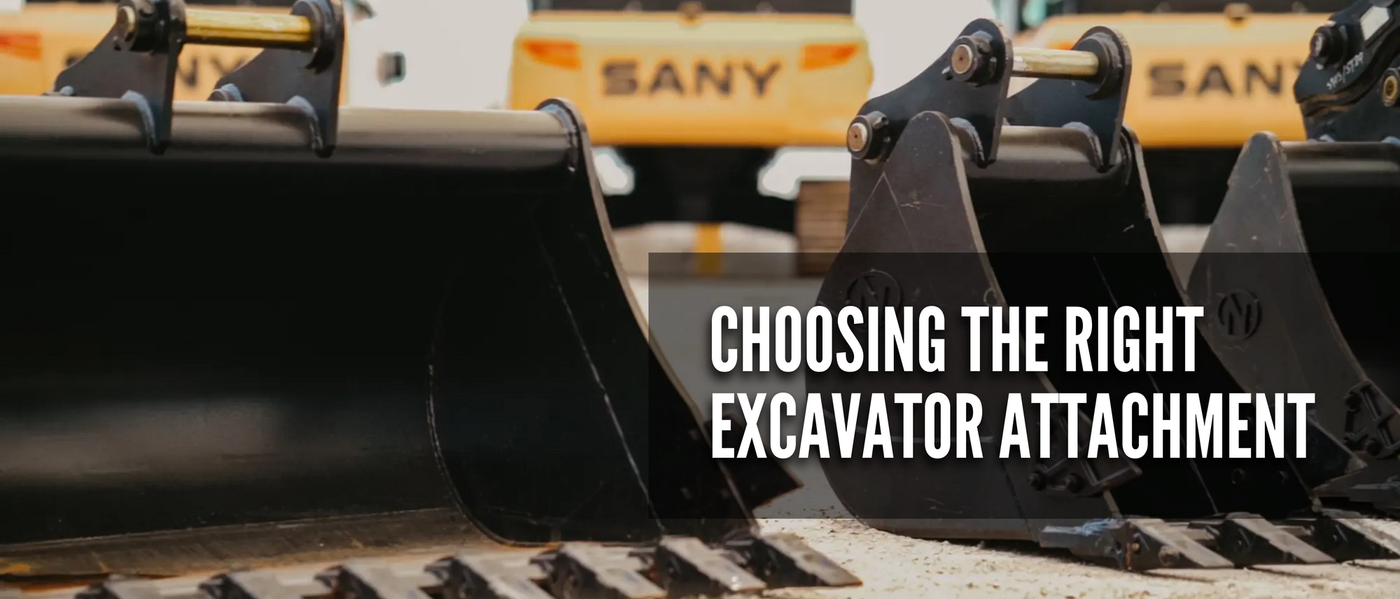
There are dozens of options for excavator attachments. Some are pretty straightforward, but others are more open-ended and could be used in various ways. Depending on your industry, you might have particular needs for an attachment.
You’ll also find that attachments can go by many names, which change based on region and job site.
So here are some standard excavator attachments, what we call them, and how we’ve seen them used.
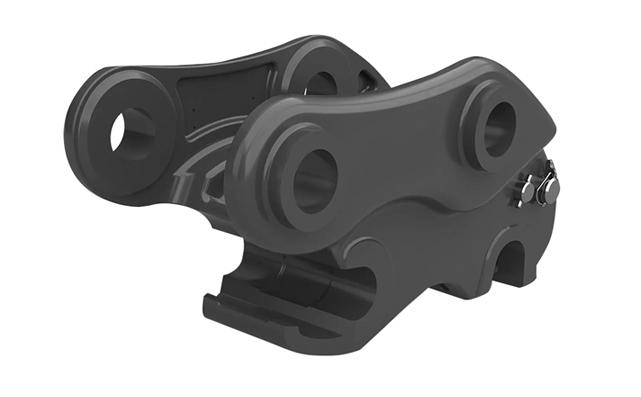
Couplers
Couplers for excavators, also known as quick couplers, quick connects, or quick hitches, are mechanical or hydraulic devices that attach excavator attachments quickly. They make it easier to connect and disconnect different attachments, such as buckets, hammers, and other tools, to what’s sometimes referred to as the excavator's arm or the stick.
Check out this overview of hydraulic couplers:
Types of Couplers for Excavators
Mechanical Couplers: Mechanical couplers are manually operated and use pins or latches to secure the attachment to the excavator. The operator manually inserts the pins or engages the latches to lock the attachment in place. The operator must manually disengage the pins or latches to release the attachment. Based on the size of the machine, it can take more than one person to disengage the pins. If it’s an especially large machine, a sledgehammer might be involved to get the pin out. So on larger machines, we’d suggested a hydraulic coupler to make things more efficient.
Hydraulic Couplers: Hydraulic couplers use hydraulic cylinders to connect and disconnect attachments from the excavator. The operator can control the coupler from the cab, engaging or disengaging the attachment without leaving the operator's seat.
Advantages of Using Excavators Couplers
- Time Savings: Quick couplers significantly reduce the time required to change attachments, improving productivity and efficiency on the job site.
- Operator Convenience: With quick couplers, the operator can switch between various attachments without leaving the cab, providing greater comfort and convenience.
- Versatility: Couplers allow excavators to use a wide range of attachments, increasing the machine's versatility/profitability and making it suitable for multiple tasks.
- Safety: Quick couplers reduce the need for manual handling of heavy attachments, which can enhance safety by minimizing the risk of accidents and injuries.
- Compatibility: Many quick couplers are compatible with multiple brands and models of excavators, allowing for more flexible use of attachments across different machines.
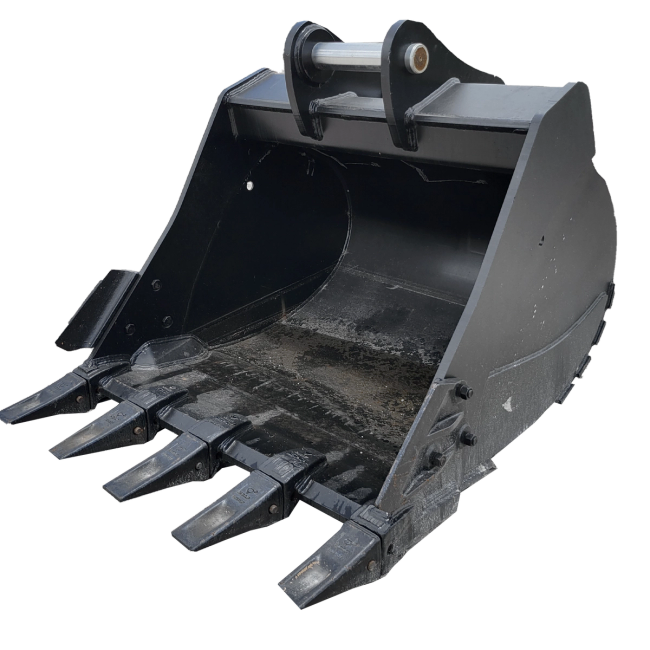
Buckets
Bucket attachments for excavators are among the most common and essential tools used in construction, excavation, and earthmoving projects. Buckets come in various sizes and designs for specific tasks and applications. They’re attached to the excavator's stick and can dig, scoop, and move various materials, such as soil, gravel, sand, and rocks.
Types of Bucket Attachments for Excavators
Standard Excavator Bucket: Standard buckets, also known as general-purpose buckets or digging buckets, are the most common type. They come in various sizes, are easily identified with their large teeth, and are suitable for general digging, loading, and material handling tasks.
Heavy Duty Bucket: Heavy-duty buckets, or heavy-duty digging buckets, are designed with reinforced structures and thicker steel to withstand more robust digging and loading conditions. They’re ideal for handling denser and tougher materials and terrain.
Rock Bucket: Rock buckets have special features, such as additional wear plates and stronger teeth, to provide extra durability when digging in rocky terrain.
Ditch-Cleaning Bucket: Ditch-cleaning buckets, ditching buckets, grading buckets, or mud buckets have a unique wide and shallow design, often resembling an elongated scoop. It's engineered for efficient excavation and shaping of ditches, trenches, and waterways. The bucket's profile allows it to move quickly and shape larger volumes of soil, making it particularly useful for tasks that involve creating or maintaining drainage systems, channels, and similar linear excavations.
Skeleton or Grapple Bucket: Skeleton or grapple buckets have openings or spaces between the tines, allowing fine materials like soil to fall through while retaining larger debris like rocks and logs. There are different types of grapples (i.e. root, rock, rake, etc.) depending on what you need it for.
Tilt Bucket: Tilt buckets have a tilting mechanism that allows the bucket to tilt left and right, providing enhanced flexibility for shaping slopes, grading, and ditch cleaning. You’ll find them with a straight edge.
Padding or Screening Bucket: These sort and separate materials on-site, allowing the operator to retain valuable material while removing debris and unwanted particles during excavation and material handling tasks.
Trapezoid bucket: A trapezoid bucket gets its name from its unique trapezoidal shape. These buckets dig and grade materials while maximizing the bucket's capacity. The sloping sides of the bucket allow for better material retention and smoother cutting through the ground during excavation tasks. These are sometimes called V-shaped buckets or V-ditch buckets and used in ditching, trenching, and pipeline work.
Advantages of Using Buckets
- Versatility: Bucket attachments are versatile tools capable of handling various materials and tasks, making them essential for different construction and earthmoving projects.
- Efficiency: Buckets allow excavators to dig and move materials efficiently, reducing the manual labor required. Using the right bucket will save you time and money.
- Time Savings: Operators can quickly load and unload materials using buckets, improving overall project efficiency and timelines.
- Cost-Effectiveness: Bucket attachments are relatively inexpensive compared to other specialized attachments, making them a cost-effective solution for many tasks.
- Easy to Use: Bucket attachments are easy to install and use, and most excavator operators are familiar with their operation.
Using the right bucket is important for efficiency. If you’re using a bucket that’s not quite right, it could take longer (and cost more money).
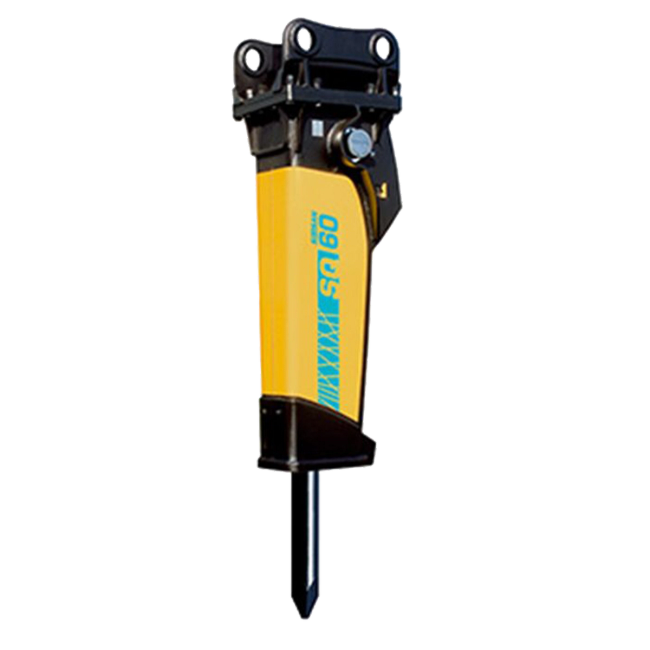
Hammers
Hammers for excavators, also known as hydraulic breakers or rock breakers, are powerful attachments designed to break through hard materials such as rock and concrete. They’re used in construction, demolition, quarrying, and mining to break up tough materials so they can be moved more efficiently.
How Excavator Hammers Work
Hammers for excavators operate based on a hydraulic system. The attachment connects to the excavator's hydraulic system, which provides the necessary power to use the hammer. The hydraulic system drives a piston inside the cylinder, which creates powerful forces to break concrete, rock, and other hard materials.
Pressurized hydraulic oil is directed to the piston when the operator activates the hammer, causing it to move up and down rapidly. The movement of the piston generates intense impact energy that moves to the chisel or tool bit at the front of the hammer. The chisel strikes the surface repeatedly at high speed and heavy force, breaking the material into smaller pieces.
Advantages of Using Hammers for Excavators
- Efficiency: Hammers can break through hard materials quickly, increasing productivity and efficiency in various construction and demolition tasks. They might be more expensive than a bucket, but even renting a hammer can save money on time and labor.
- Versatility: Hammers are versatile attachments suitable for breaking rock, concrete, and other dense materials.
- Reduced Vibration: Modern hammers are designed with dampening systems to reduce vibration and minimize strain on the excavator and the operator.
- Precise Control: Operators can precisely control the impact force and frequency of the hammer, allowing for accurate and controlled demolition work.
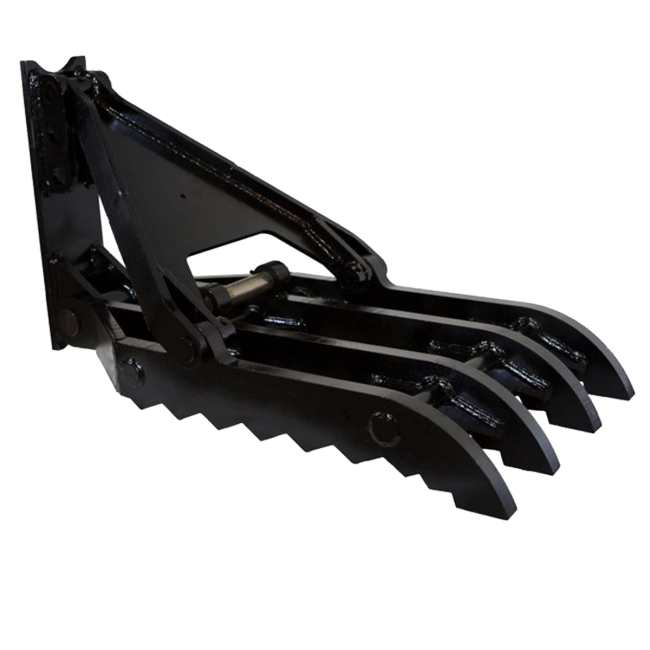
Thumbs (Long and Short)
Excavator thumbs are mechanical or hydraulic attachments mounted to the bucket. They provide better grip and control when handling objects like rocks, tree stumps, or irregularly shaped items. If a bucket is the palm and fingers of a hand, the thumb is…the thumb.
Thumbs are handy when working with irregularly shaped objects, loose materials, or when you need precise control during excavation and material handling.
1. Long Thumbs (Mechanical or Hydraulic)
Long thumbs are hydraulic-powered attachments that are used when the machine is equipped with a quick coupler. They’re typically mounted to the excavator's stick and can be adjusted and positioned using a hydraulic cylinder. Long thumbs are versatile and are needed if the machine has a quick coupler so the thumb tine will reach the bucket.
Advantages of Long Thumbs
- Efficiency: Long thumbs are necessary if your machine has a quick coupler due to the added distance between the stick and bucket. A long thumb has added length to the tines to make up for the extra distance.
- Enhanced Grasping: Long thumbs provide a larger range of motion, enabling the excavator to securely grip and handle materials like logs, rocks, pipes, and irregularly shaped objects.
- Precise Control: Hydraulic control allows for fine adjustments, ensuring accurate positioning and secure gripping of materials.
- Increased Versatility: Long thumbs can be used in many ways, like sorting, stacking, and material handling.
2. Short Thumbs (Mechanical or Hydraulic)
Short thumbs can be mechanical or hydraulic and are used on machines without a quick coupler. Mechanical thumbs or rigid thumbs, have a base plate welded to the excavator’s stick and are non-hydraulic attachments fixed in position. Hydraulic thumbs are typically mounted to the excavator's stick or arm and can be adjusted and positioned using a hydraulic cylinder.
Advantages of Short Thumbs
- Efficiency: Short thumbs are used on machines not equipped with a quick coupler and allow the operator to handle objects like rocks, tree stumps, or irregularly shaped items.
- Precise Control: Hydraulic control allows for fine adjustments, ensuring accurate positioning and secure gripping of materials.
- Increased Versatility: Short thumbs can be used in many ways, like sorting, stacking, and material handling.
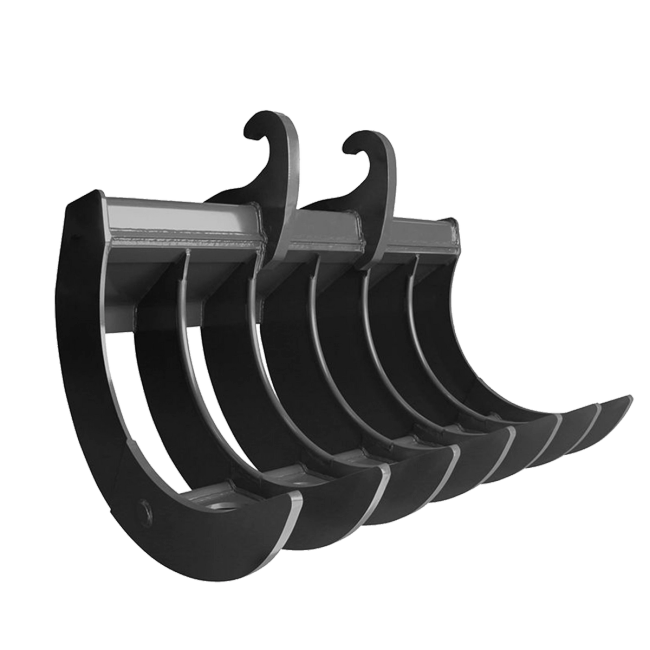
Root Rakes
Root rakes, also known as rakes or land-clearing rakes, are tools designed to efficiently clear, gather, and move vegetation, rocks, debris, and other materials. These attachments are used in land clearing, forestry, site preparation, and landscaping projects where vegetation or rocks need to be removed or managed.
Features of Rake Attachments for Excavators
Tines or Teeth: Rake attachments have multiple sturdy tines or teeth spaced across a wide bar. Depending on the specific application, these tines, such as straight, curved, or serrated, can vary in design.
Open Design: Rake attachments typically have an open structure that allows debris to be collected and retained while allowing fine materials like soil to fall through.
Hydraulic Control: Rake attachments use the hydraulic power of the bucket cylinder to allow the operator to adjust the angle and position of the rake, providing control during operation.
Advantages of Using Rake Attachments
- Efficient Land Clearing: Rake attachments are an excellent choice for clearing vegetation, shrubs, small trees, and debris from construction sites or overgrown areas.
- Versatility: Rake attachments can handle various materials, making them suitable for multiple tasks, including land clearing, site preparation, storm cleanup, and agriculture.
- Selective Sorting: Rake attachments can selectively pick up and remove specific materials, making them useful in environmental restoration and habitat management projects.
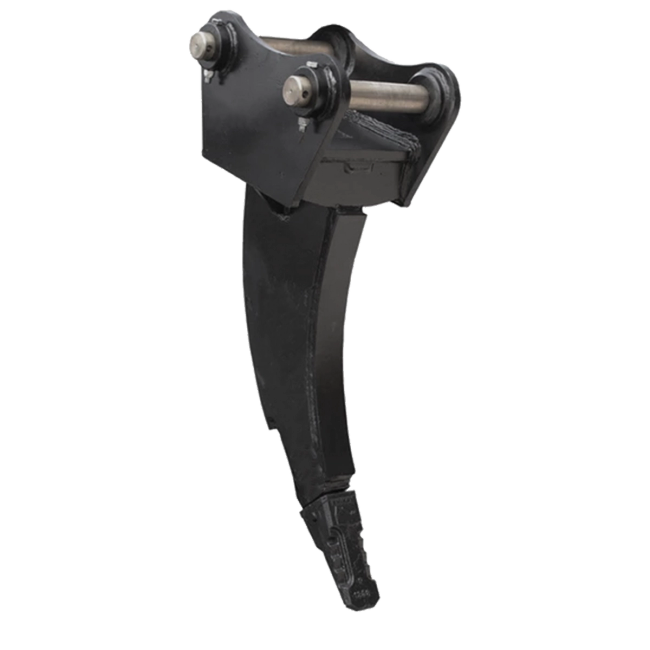
Rippers
Rippers for excavators, also known as excavator rippers or frost rippers, break up hard or compacted materials in earthmoving, excavation, and land development projects. They’re beneficial when dealing with tough materials like rock, frozen ground, asphalt, or hard clay that standard digging buckets may struggle to penetrate.
Features of Rippers for Excavators
Single or Multiple Tines: Rippers can have single or multiple tines (or teeth) arranged in a shank-like structure. The number and design of the tines depend on the specific use and the level of force required.
Heavy-Duty Construction: Rippers are built with reinforced and durable materials to withstand the impact and force exerted during ripping operations.
Pointed Tips: The tines of rippers typically have pointed or chisel-like tips to penetrate hard materials easily.
Hydraulic Control (Optional): Some rippers can be equipped with hydraulic cylinders for adjustable penetration depth, allowing the operator to control the ripping force based on the material's hardness.
Advantages of Using Rippers for Excavators
- Breaking Hard Materials: Rippers are great at breaking up hard or compacted materials that standard digging buckets may struggle with.
- Cost-Efficient: Using a ripper attachment can save time and fuel by reducing the need for repeated digging attempts with a bucket.
- Versatility: Rippers can be used in various ways, including rock excavation, trenching in tough soil, and ripping up concrete, roots, or frozen ground.
- Preparation for Other Equipment: Ripping the ground can prepare it for other equipment or construction processes, such as blasting or additional excavation.
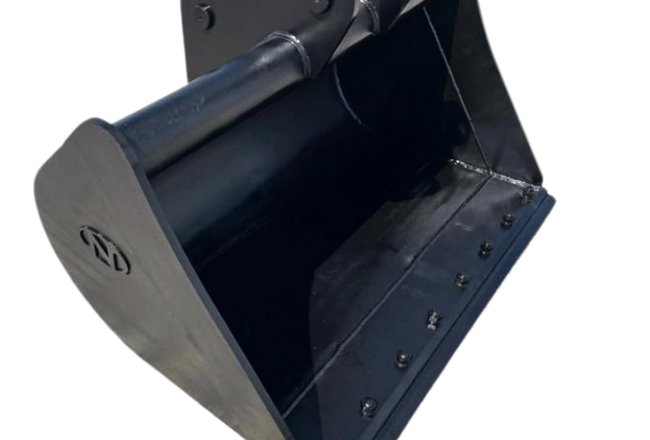
Ditch-Cleaning Buckets
Ditch-cleaning buckets for excavators excavate, shape, and clean ditches, channels, and waterways. These buckets have a unique shape and features that make them ideal for efficient and precise ditching operations. You’ll find them in construction, road maintenance, landscaping, and water management projects.
Features of Ditch-Cleaning Buckets
Curved Design: Ditch-cleaning buckets have a curved shape that matches the contours of ditches and channels, ensuring efficient material removal and shaping.
Extended Width: These buckets are typically wider than standard buckets, providing a larger capacity for removing more material with each pass.
High Back and Heel: Ditch cleaning buckets have a higher back and heel than standard buckets, allowing them to retain material better during excavation and reducing spillage.
Longer Bottom: The bottom of the bucket is longer, helping to smooth out and shape the ditch as the excavator moves along the length of the channel.
Drainage Holes: Some ditch cleaning buckets have drainage holes to allow excess water to flow out, preventing added weight during the operation. These are often referred to as mud buckets.
Reinforced Cutting Edge: The bucket's cutting edge is often reinforced with wear-resistant materials to withstand the abrasive nature of ditch materials.
Advantages of Using Ditch Cleaning Buckets
- Efficient Ditching: The curved design and extended width allow for faster and more efficient ditching, reducing the time and effort required for the task.
- Precise Shaping: Ditch-cleaning buckets can shape ditches more precisely, achieving the desired dimensions and slopes for adequate water flow.
- Reduced Material Loss: The higher back and heel of the bucket minimize material spillage during excavation, reducing the need for rework.
- Enhanced Drainage: Ditch-cleaning buckets help create well-formed ditches that improve water drainage, reducing the risk of flooding and erosion.
- Versatility: These buckets can serve a few purposes, such as ditch cleaning, grading, shaping embankments, and creating drainage channels.
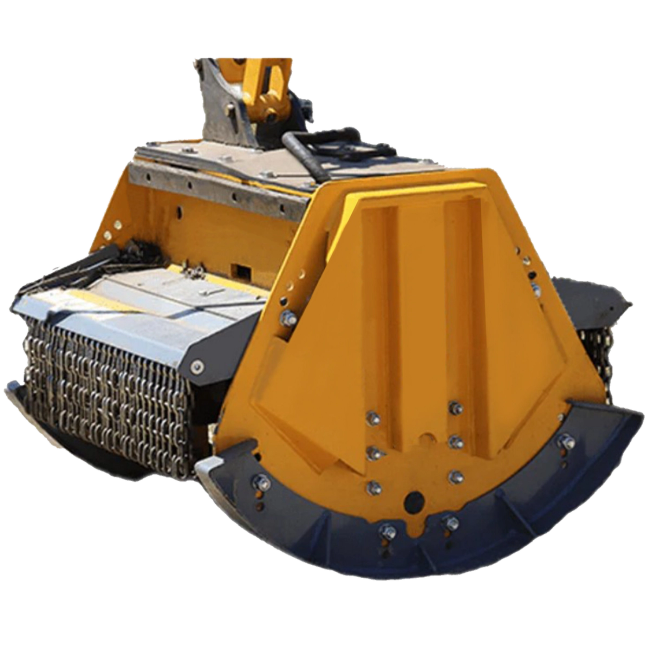
Mulchers
Mulchers for excavators, also known as excavator-mounted forestry mulchers or mulching heads, clear vegetation, undergrowth, and small trees in forestry and land-clearing applications. These attachments are used in projects where large areas need to be cleared of dense vegetation and trees to make way for development or to maintain land for agricultural or environmental purposes.
How Mulchers for Excavators Work
Mulchers for excavators have a heavy-duty rotating drum with cutting teeth or hammers that shred and mulch vegetation. The attachment connects to the excavator's hydraulic system, which powers the drum and allows the operator to control its movements.
To use the mulcher, the excavator operator positions the attachment over the vegetation to be cleared. The rotating drum's cutting teeth or hammers reach the vegetation, cutting and grinding it into small pieces. As the drum spins, it continues to shred the foliage, leaving a layer of mulch on the ground.
Advantages of Using Mulchers for Excavators
- Fast and Efficient Clearing: Mulchers can clear large areas of vegetation quickly, making them highly efficient for land-clearing projects.
- Versatility: Mulchers can handle a wide range of vegetation, from dense underbrush to small trees.
- Environmentally Friendly: Mulching vegetation on-site returns organic material to the soil, promoting soil health. It also reduces the need for burning or transporting debris for disposal.
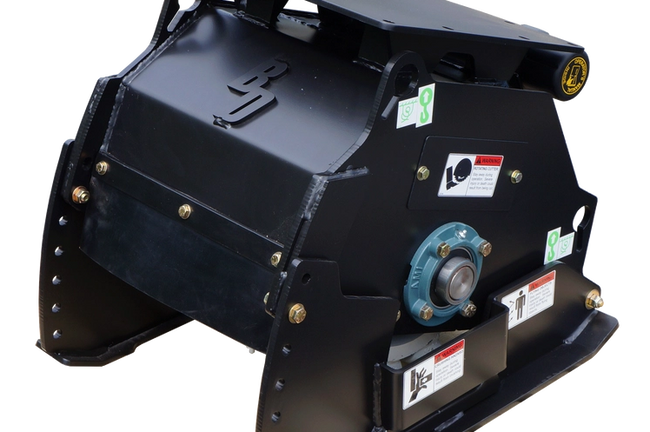
Cold Planers
Cold planers, also known as cold milling machines or asphalt milling machines, remove layers of old asphalt or concrete surfaces from roads, parking lots, and other paved areas.
How Cold Planers for Excavators Work
Cold planers connect to the excavator's stick using a coupler or quick connect. With the planer over the surface, the operator activates the cold planer to start the milling.
The cold planer has a rotating cutting drum with teeth. It mills the asphalt or concrete surface, breaking it into small pieces. These pieces are moved by the planer's conveyor system to a collection area or dump truck for disposal.
The depth of the milling cut can be adjusted using hydraulic controls, allowing the operator to remove the desired thickness of the surface layer.
Advantages of Using Cold Planers for Excavators
- Surface Restoration: Cold planers remove damaged or deteriorated surfaces, providing a clean and even base for repaving or overlaying.
- Accurate Milling: Cold planers offer precise milling control, allowing for accurately removing specific depth and width.
- Reduced Material Waste: Milling the surface rather than traditional removal methods minimizes material waste, making it a more eco-friendly process.
- Efficiency: Cold planers can quickly remove large areas of damaged pavement, speeding up road repairs.
- Cost-Effectiveness: Cold planers help extend the lifespan of existing roads by removing damaged layers and allowing for cost-effective repair and maintenance.
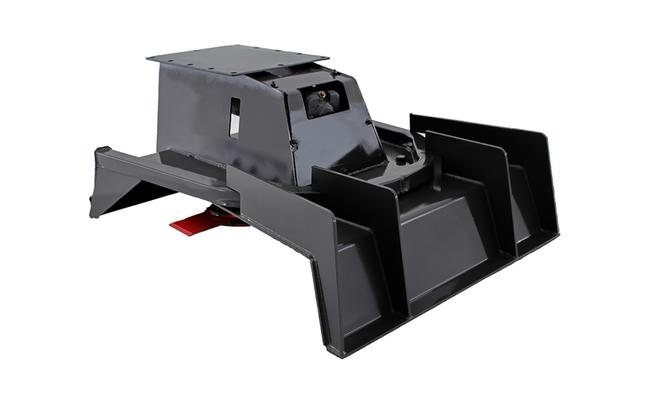
Brush Mowers
Brush mowers, or excavator-mounted brush cutters, cut and clear dense vegetation, thick brush, and small trees. These attachments are used in land clearing, forestry, right-of-way maintenance, and vegetation management projects. They allow excavators to handle vegetation in areas where traditional mowers or land-clearing equipment might not be practical.
How Brush Mowers for Excavators Work
Brush mowers for excavators consist of heavy-duty blades, much like a lawn mower. The attachment connects to the excavator's hydraulic system, which provides the power needed to rotate the blades and control its movements.
To operate the brush mower, the excavator operator positions the attachment near the vegetation to be cleared. The blades are activated, and the blades rapidly spin and engage with the foliage, cutting and mulching the brush into small pieces. The operator can maneuver the excavator to cut vegetation at different angles and clear the area as needed.
Advantages of Using Brush Mowers for Excavators
- Versatility: Brush mowers for excavators can handle a wide range of vegetation, including dense brush, small trees, saplings, and other tough vegetation.
- Efficiency: These attachments are highly efficient in quickly clearing large vegetation areas, making them suitable for land clearing and right-of-way maintenance projects.
- Accessibility: Excavator-mounted brush mowers can access clear vegetation in challenging terrain, steep slopes, and areas with limited ground access where traditional mowers might not operate.
- Mulching Capability: Brush is cut and mulched simultaneously into smaller pieces, which helps reduce the volume of vegetation and creates mulch that can decompose back into the soil.
- Safety: Clearing vegetation with a brush mower minimizes the risk of fire hazards and reduces the presence of potential hiding spots for pests and animals.
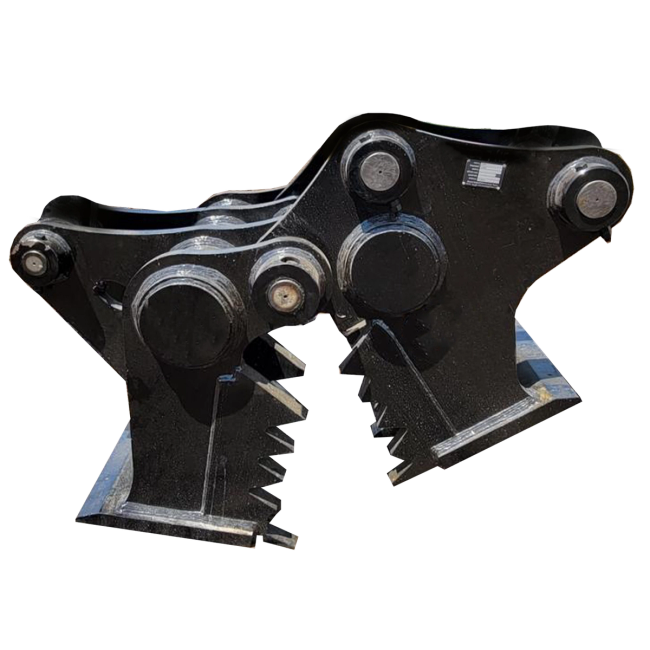
Concrete Pulverizers
Pulverizers, sometimes called concrete crushers, are powerful attachments that break down and crush concrete structures and other hard materials. They’re used in construction, demolition, and recycling applications. The primary purpose of a pulverizer is to reduce large concrete chunks into smaller, more manageable debris, allowing for easier disposal, recycling, or reuse.
How Concrete Pulverizers Work
Concrete pulverizers for excavators typically consist of a heavy-duty fixed jaw and a movable jaw or two opposing jaws. The fixed jaw is mounted on the excavator arm or stick, while the movable jaw is attached to the excavator's hydraulic system. The jaws exert significant force and pressure on the concrete or other material to crush it.
Pulverizer Advantages
- Versatility: Pulverizers can handle various materials, including concrete, reinforced concrete, masonry, rocks, and other hard materials, making them versatile attachments for various demolition and construction tasks.
- Efficiency: The powerful crushing force of pulverizers allows for quick and efficient demolition of structures, reducing the time required for manual demolition methods.
- Reduced Waste: By breaking down large concrete pieces into smaller pieces, pulverizers reduce the volume of waste generated during demolition, making it easier to manage and dispose of the debris.
- Cost Savings: Using a pulverizer can save on disposal costs, as crushed materials can often be recycled or used on-site for fill material.
Other Types of Attachments
Like we said, you can add dozens of different attachments to your excavator for ease and efficiency. Here are some of the other attachments you can add to your excavator.
Snow Attachments
Snowplows and snowblowers can be mounted on excavators for snow removal and winter maintenance tasks.
Magnet Attachments
Magnet attachments can pick up and move metal objects, making them useful in recycling yards and construction sites.
Compactors
Compactor attachments can compact soil, gravel, or other loose materials to create a stable surface. They’re used in road construction and landscaping projects to improve the stability and load-bearing capacity of the compacted surface.
Shears
Also known as hydraulic or demolition shears, shears cut through and demolish various materials, including metal structures, concrete, rebar, and other tough materials. You can find them in demolition, recycling, and construction projects requiring precise cutting and dismantling.
Tiltrotators
Tiltrotators are sophisticated hydraulic attachments designed to enhance the versatility and efficiency of the excavator's digging and material handling capabilities. A tiltrotator combines two essential functions: tilt and rotation. It allows the bucket or attachment to rotate (spin around its axis) and tilt (pivot up and down) with hydraulic control, providing the excavator with unmatched flexibility and precision in various tasks.
Stump Grinders
Stump grinders remove tree stumps and their root systems from the ground. These attachments are all stars in landscaping, forestry, and land-clearing projects. Stump grinders offer an efficient and effective way to eliminate tree stumps, allowing for smoother site preparation and preventing potential hazards caused by leftover stumps.
Grapples
Grapples grip and handle various materials such as logs, rocks, demolition debris, and scrap metal. Excavator grapples are used in forestry, construction, demolition, and waste-handling to improve material handling efficiency and productivity. The grapple type can vary, with options like fixed, rotating, and hydraulic grapples.
Multiprocessor
Multiprocessors for excavators are versatile attachments designed to perform multiple demolition tasks with a single tool. They’re used in the demolition and recycling industries to efficiently process and sort different materials. A multiprocessor typically consists of interchangeable jaws or crusher arms, allowing the excavator operator to quickly switch between various functions without changing the entire attachment.
Forks
Excavator forks or material handling forks lift, carry and transport various materials and objects on construction and industrial job sites. These forks attach to the excavator's boom or quick coupler, transforming the machine into a versatile material handling tool.
Augers
Augers for excavators are specialized attachments designed for drilling holes in the ground. They consist of a rotating helical screw-like drill bit, commonly known as an auger, attached to the end of the excavator's stick. The excavator's hydraulic system powers the auger's rotation, allowing it to dig into the soil, rock, or other materials.
Post drivers
Excavator post drivers install posts or poles into the ground quickly and efficiently. You’ll see them in construction, fencing, agriculture, and where the installation of posts is required. Post drivers for excavators streamline the process of driving posts, reducing manual labor and improving productivity.
Concrete grinders
Concrete grinders grind and smooth concrete surfaces. They’re used in construction and renovation projects to prepare concrete surfaces for polishing, coatings, or resurfacing. Concrete grinders for excavators provide a highly efficient and versatile concrete surface preparation and finishing solution.