What to Know About Renting Heavy Equipment
- News
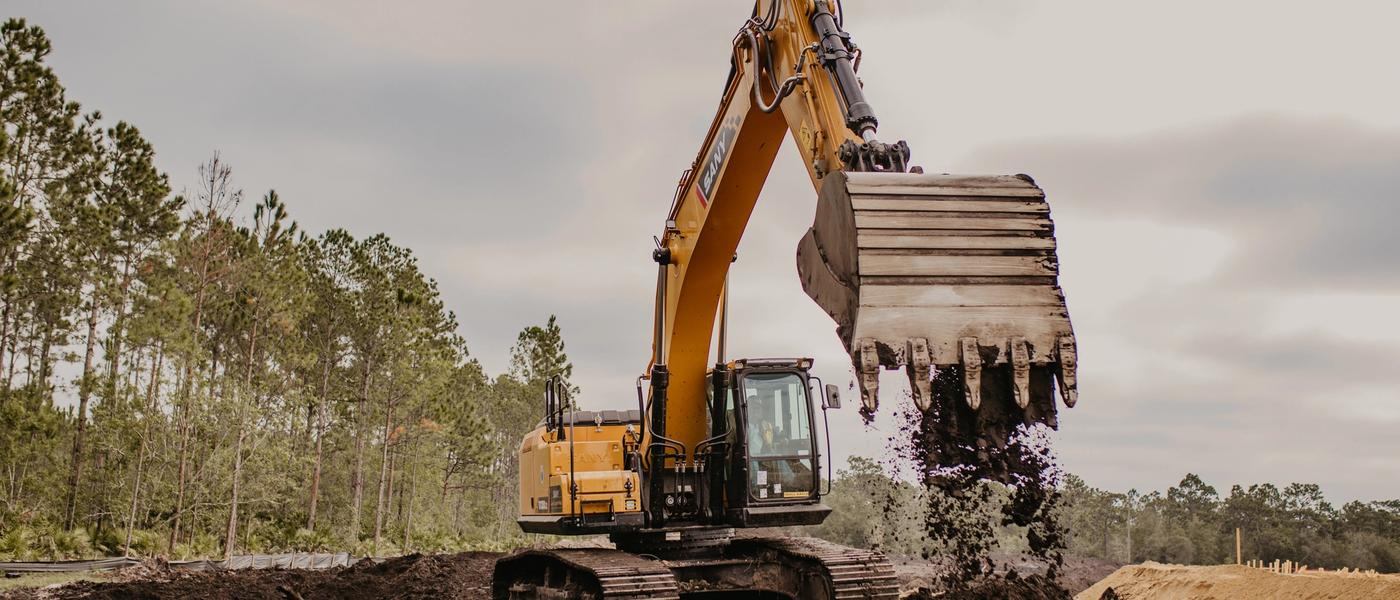
Considering renting heavy equipment? Making the right decisions in the rental process is crucial to ensure efficiency, safety, and cost-effectiveness. This guide offers insights and tips on what to look for, how to navigate rental agreements, and steps to ensure a smooth equipment rental experience.
Determine which machines you need
Before getting into a heavy equipment rental, you must understand precisely what machinery you need for your project. Making the right decision can save you time and money and avoid potential project delays. Some of you reading will know this, but if you’re starting a new project or want to learn more, here's a guide to help you determine the best fit:
Nature of the Project
Start by clearly defining the scope and nature of your project. For instance, excavators are perfect for digging, grading, and lifting, while skid steers are versatile machines often used for digging, drilling, and pushing material. The size and depth of excavation, the type of soil or material you're working with, and the space constraints can all influence the type of equipment you need.
Duration of the Project
The time you'll need the machine can also determine the type. Some machines may be more cost-effective for short-term projects, while others might be better suited for prolonged use.
Machine Specifications
Once you've identified a potential machine, delve deeper into its specifications. Look at factors like horsepower, digging depth, lifting capacity, and any attachments that might be beneficial. Ensure the equipment can handle the workload and conditions of your project.
Research and Reviews
It's the age of information, and there's likely a trove of data online about almost any machine you're considering. Look for reviews from other professionals who've used the equipment in similar conditions. Their insights can guide your decision.
Safety and Compliance
Ensure that the machinery you're considering meets your area's safety standards and compliance regulations. Some machinery might have specific emissions standards or safety features that are mandatory.
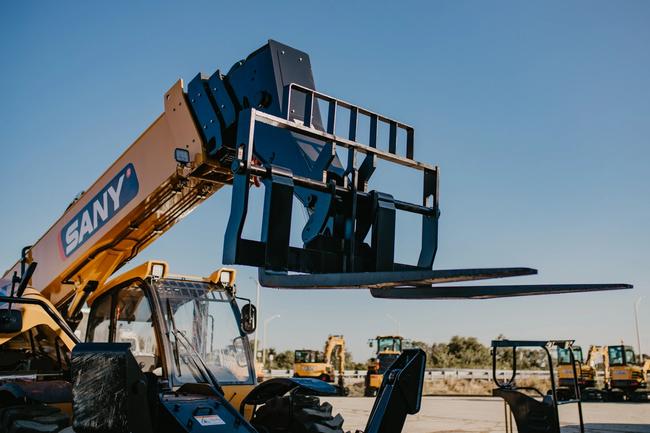
Read the rental agreement for full terms and conditions
The rental agreement is the binding contract between you and the rental company. It outlines the responsibilities, charges, and expectations for both parties. Overlooking or misunderstanding any part of this agreement can lead to unexpected costs, disputes, or even legal actions. Here's a closer look at some essential sections:
Insurance
Insurance is pivotal when renting heavy machinery. Damage to the equipment, or caused by the equipment, can result in hefty bills. Make sure to understand the following:
- Coverage: Does the rental company provide insurance? If so, what does their insurance cover? Does it only cater to damages to the machine, or does it extend to property damage or third-party injuries caused by the equipment?
- Your Responsibility: How much are you liable for in the event of damage? There might be a deductible or an amount up to which you're responsible before the insurance kicks in.
- Additional Insurance: Your current business insurance may cover equipment rentals. Check with your provider. If not, you might need additional coverage through the rental company or another provider.
At Newman Tractor, we require all renters to provide their own machine insurance.
Maintenance
Maintaining the machinery is crucial to ensure it operates efficiently and safely. Understand your role in this:
- Routine Checks: Some rental agreements stipulate that the renter is responsible for daily or regular checks on fluid levels, tire pressure, and other routine inspections.
- Repairs: If there's a malfunction or breakdown, what's the protocol? Are you required to notify the rental company immediately, or can you conduct minor repairs on your own?
- Wear and Tear: Normal wear and tear is expected, but excessive wear might incur extra charges. Understand what the rental company considers " normal " to avoid surprises.
We prefer to maintain our rental machines at Newman Tractor. But if that’s not practical, we’ll help you work with an outside vendor to maintain the machine properly.
Delivery and Pick Up
Logistics are a significant part of the rental process, impacting your project's timeline and budget:
- Delivery Costs: Ensure you're clear on these costs upfront. Some companies offer a flat fee, while others charge based on distance.
- Timeline: Know the expected delivery time. If the machinery arrives late, it can delay your project. Some contracts offer concessions or discounts for late deliveries.
- Pick-Up Protocol: What's the return process when you're done with the equipment? Do you need to clean it? Refuel it? Also, understand the costs or penalties associated with late returns (we’ll talk more about that later).
- Drop-Off Location: Some companies might allow for different drop-off locations, especially if they have multiple branches. This can be convenient and potentially reduce transport costs if your project moves sites.
We work with you to coordinate delivery to your job site, wherever possible. Or hey, if you’ve got the equipment to haul your rental, we’ll help you load it up.
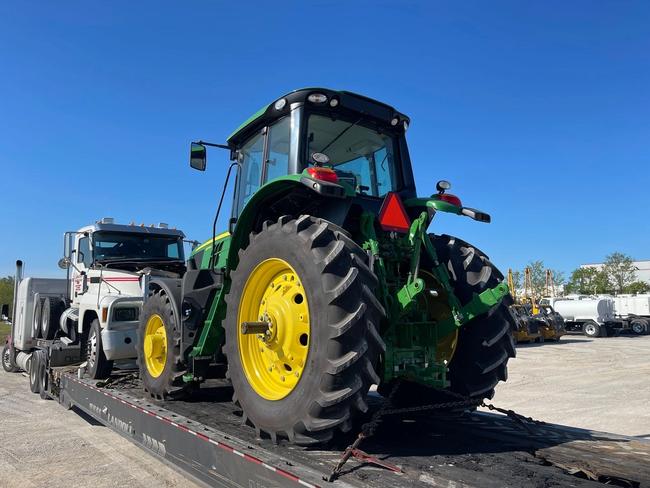
Inspect the Machine
Whenever you rent heavy equipment, a thorough inspection is crucial before using and returning it. This process helps identify any existing damages, ensures the machine is in good working condition, and prevents being held liable for issues you didn't cause. If the first time you see the rental will be when it’s delivered to a job site, be sure to do this ASAP.
Exterior Inspection
- Paint and Surface: Look for scratches, dents, or rust. These can indicate wear and tear or potential structural issues.
- Tires/Tracks: Examine the tires or tracks for wear. Ensure tires are properly inflated and look for any signs of damage or embedded objects.
- Attachments: If the machine comes with any attachments, make sure they are secure and in good condition.
Operational Test:
- Controls: Ensure all levers, switches, and controls are functioning correctly.
- Engine: Listen for any unusual sounds when starting and running the machine. Check for smooth transitions when changing speeds or directions.
- Brakes: Test the brakes to ensure they're responsive and effective.
- Lights and Indicators: If the machinery has lights or indicators, ensure they're operational.
Fluid Check
- Oil Level: Check the engine oil level and note its color. Dark or dirty oil can indicate the need for a change.
- Coolant: Ensure the coolant level is appropriate to prevent overheating.
- Hydraulic Fluid: For machinery like excavators, hydraulic fluid is critical. Check for appropriate levels and any signs of leaks.
Documentation
- Pre-Existing Damage: Ensure any damage or issues identified are documented before using the machine.
- Photographs: Taking photos can be a good practice. It provides a visual record of the machine's condition at the start and end of the rental period.
Safety Features
Ensure all safety features, like alarms, mirrors, and safety belts, are in place and functional.
Feel free to ask the rental company if you're unfamiliar with a particular machine or notice something unusual. It's better to clarify doubts upfront than face challenges during your project.
Remember, a thorough inspection is not just about protecting yourself from extra charges. It's about ensuring the equipment you're renting is safe and fit for purpose, which is vital for your project's successful and timely completion.
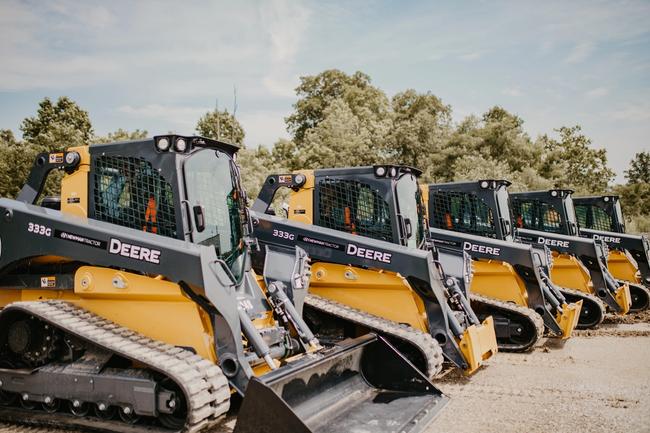
Secure Your Rental Equipment
Protecting your rented heavy equipment from theft, vandalism, and unintended damages is crucial. Not only does this save you from potential replacement or repair costs, but it also ensures that your project timeline remains on track. Here are some fundamental steps to ensure your equipment's security.
Understand the Expenses
Renting heavy equipment may seem straightforward, but several associated costs can influence your project's budget. Understanding these expenses beforehand can prevent surprises and help you allocate funds more efficiently.
Deposits
Rental companies can require a deposit upfront (but not all), a security measure against potential damages or contract breaches.
Some deposits are fully refundable upon return of the equipment in proper condition, while others may have a non-refundable portion.
Understand the circumstances under which the company might deduct amounts from your deposit, such as minor damages, cleaning fees, or fuel charges.
Fuel
Fuel consumption can be a significant cost, especially for larger machines and long-term projects.
- Check if the machine needs to be returned with a full tank or if you're billed for the fuel used.
- Machines with better fuel efficiency can save costs in the long run.
- Ensure you know whether the equipment uses diesel, gasoline, or another type of fuel to avoid using the wrong one, which can lead to damage.
Storage
Where you keep the equipment when it's not in use can also have associated costs.
- On-Site Storage: If you're storing the equipment on the project site, consider security and protection measures, which might have costs.
- Off-Site Storage: In some cases, storing the equipment at a dedicated facility might be more efficient, especially between project phases. Check local storage rates.
Extra Fees
Beyond the standard rental fee, additional charges might incur on various circumstances.
- Late Returns: If the equipment is returned after the stipulated time.
- Damages: Beyond normal wear and tear, any damage to the equipment will likely result in repair charges.
- Cleaning Fees: Some companies might charge a cleaning fee if the equipment is returned excessively dirty (so clean it before you return it).
- Cancellation Fees: There might be a cancellation fee if you cancel the rental after a certain point. This all depends on who you’re renting from.
Being aware of all potential costs allows for more accurate budgeting and ensures that unexpected financial hurdles don't stall your project. Always clarify any ambiguities in the rental agreement to be particular about the expenses you're incurring.
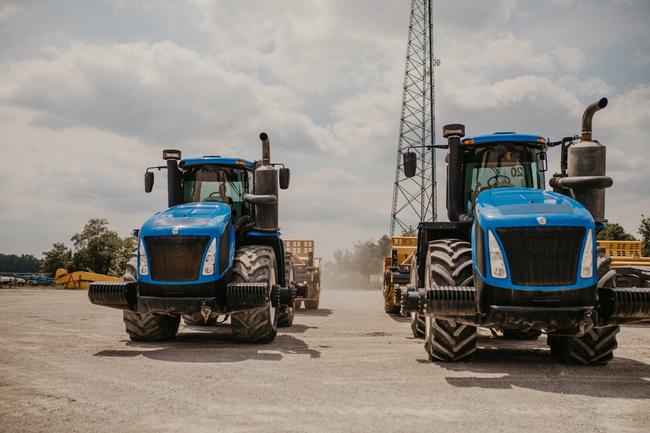
Ensure Emergency Support
Whether it's equipment malfunction, sudden breakdowns, or any other unexpected events, having a solid emergency support system can make the difference between minor setbacks and significant project delays.
When an accident involving rented heavy machinery, immediate action is essential to ensure everyone's safety, protect the equipment from further damage, and comply with legal and contractual obligations.
A comprehensive emergency support plan can help mitigate risks, reduce downtime, and ensure the safety and efficiency of your operations. Always prioritize companies that demonstrate a solid commitment to customer support and safety.
We offer a 24-hour emergency service repair line for after hours, in case anything should happen.
Keep it in Good Condition
Renting heavy equipment can be a significant investment, and maintaining its condition is not just a contractual obligation but also a way to ensure seamless operations. Here's how to ensure the equipment remains in top shape:
Routine Checks and Regular Maintenance
- Before starting the machinery, perform a routine check to ensure all parts are functioning correctly. Look for signs of wear, leaks, or any unusual noises.
- Regularly check fluid levels, such as oil, coolant, and hydraulic fluid.
- Depending on the rental duration, the machinery might require routine maintenance, like oil changes or replacing specific parts.
- Coordinate with the rental company on these tasks. They might handle them or provide guidelines on how you should proceed.
Cleanliness
- Dirt and debris can affect the performance and lifespan of machinery. Ensure the equipment is cleaned regularly, especially after tasks that expose it to dirt or mud.
- Make sure air filters are clean and replaced when necessary. This prevents the engine from straining and reduces wear.
Operate Properly
- Only trained and certified personnel should operate the machinery. Mishandling can lead to unnecessary wear and potential damages.
- Avoid overloading or pushing the equipment beyond its recommended capacity.
Stay Within Operating Parameters
Each machine has specific operating guidelines for a reason. These guidelines help prevent faster wear and potential breakdowns and are crucial for ensuring the safety of the operator and everyone on the job site.
It's easy to feel "comfortable" when operating machinery, especially if you're trained and capable. However, comfort can be deceiving, mainly if it's a machine you don't use daily. Even experienced but younger operators can make life-threatening mistakes when they push the equipment beyond its limits.
We've heard horror stories where seemingly minor deviations from operating guidelines led to situations that could have resulted in loss of life. When operating heavy machinery, it's essential to always think about the task and how the machine will handle it. Something as simple as adding more weight could turn a routinely safe job into a dangerous situation.
So, always adhere to the operating parameters and never let your guard down. Your safety, and the safety of your team, could depend on it.
Protect from the Elements
- Extreme weather conditions, whether intense sun, rain, or snow, can affect equipment. Whenever possible, store machinery in shaded or covered areas.
- For machinery sensitive to cold, consider using engine block heaters in freezing conditions.
Report Issues Promptly
If you notice any malfunction or issue, report it to the rental company immediately. They might provide guidance or send someone to address it. Minor issues, if ignored, can escalate into significant problems that might be costlier to repair.
Use Quality Consumables
This includes using the right type and quality of fuel, lubricants, and hydraulic fluids. Low-quality or incorrect consumables can reduce performance and cause damage.
Avoid Harsh Environments
Avoid extremely dusty areas, corrosive environments, or overly wet conditions unless the equipment is designed for it. These can accelerate wear and lead to malfunctions.
End-of-Rental Check:
- Before returning the equipment, do a comprehensive check and cleanup. Ensure it's in the same condition as when rented, accounting for normal wear and tear.
- Address any minor repairs or cleaning to avoid potential additional fees from the rental company.
- Maintaining rented heavy equipment in good condition is in the best interest of your project. It ensures smooth operations, avoids unexpected repair costs, and builds trust with rental companies for future collaborations.
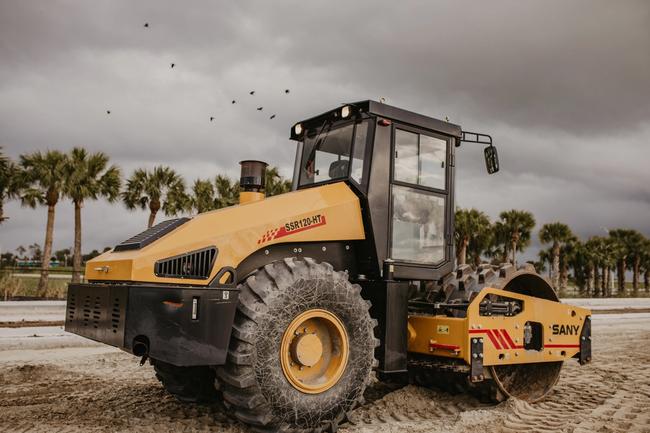
Extending Your Contract
Sometimes projects don't go as planned, or perhaps the scope changes midway, necessitating the extended use of rented equipment. Navigating this situation properly can save money, time, and potential headaches.
Contact the rental company as soon as you anticipate the need for an extension. This early communication can secure the availability of the equipment. Other clients might be waiting to rent the same equipment, so don't leave this to the last minute.
If you had procured insurance for the equipment, remember to extend the coverage period. This ensures that the machinery remains protected under the new contract duration. Failure to do so can lead to potential liabilities in damages or accidents.
Rental Purchase Options (RPO)
Rental Purchase Options, commonly called RPO, allow renters to apply a portion of their rental payments toward purchasing the equipment. This can be an attractive proposition for businesses, especially if they foresee long-term needs for specific equipment.
RPO is essentially a hybrid agreement that begins as a rental but allows the renter to purchase the equipment anytime during the rental period. Typically, a percentage of the rental payments will be credited towards the purchase price.
Why Consider RPO
- Flexibility: RPO allows businesses to decide if they want to own the equipment based on their evolving needs.
- Financial Benefits: If the equipment proves indispensable, the renter can buy it without starting from scratch, financially speaking.
- Trial Period: It offers a way to "test" equipment in real-world conditions before committing to a purchase. It’s a “try it before you buy it” situation.
Things to Consider
- Contract Clarity: Ensure that the terms of how much of the rent goes toward the purchase price are clear. This percentage can vary between contracts.
- Price Agreement: Some contracts stipulate the purchase price upfront, while others determine it based on market value at the time of purchase. Know what you're agreeing to.
- Duration: There might be a stipulated period within which you need to exercise the purchase option. Missing this window might mean forgoing the RPO benefits.
Comparison with Traditional Financing
- While RPO offers flexibility, comparing the total cost of purchasing through RPO with other financing options is essential. In some cases, traditional financing might be more cost-effective.
- Consider factors like interest rates, down payments, and the potential benefits of ownership versus renting.
Maintenance and Warranty:
If you purchase, inquire about any warranties that are still valid on the equipment.
Also, consider the machine's maintenance history. Since you've been renting it, you should have a good idea of its condition, but it's always good to conduct a thorough check before making the final purchase.
Is It Worth It? Buying vs. Renting
Buying | Renting | |
---|---|---|
Captial | Requires a significant initial investment. However, the equipment is yours once you've purchased it, adding to your company's assets. Financing options might also be available. | No significant initial investment is required. You'll typically pay a recurring fee, which can be easier on cash flow, especially for short-term projects. |
Duration and Frequency of Use | Makes more sense if the equipment will be used regularly and for extended periods. Owning might be economical in the long run if you have ongoing projects or foresee consistent use. | Ideal for short-term projects or if the equipment is needed occasionally. |
Maintenance & Repairs | Owners are responsible for all maintenance, repairs, and associated costs. This responsibility also means ensuring the equipment meets any regulatory standards. | Most rental agreements include maintenance, meaning the rental company is typically responsible for ensuring the equipment is in working order. |
Depreciation | Equipment, like other assets, depreciates over time. While it can be used as a tax deduction, the machine's value will decline, impacting its resale value. | Renters don't have to worry about depreciation since they don't own the asset. |
Flexibility | Once you own a piece of equipment, you're committed to it. Switching to a newer model or different machinery requires selling the current one and purchasing another. | Offers the flexibility to change equipment based on project needs. You can always rent the latest models or different machines as required. |
Storage | You'll need storage solutions when the equipment is not in use, which can incur additional costs. | You return the equipment once the rental period ends, freeing up space. |
Resale Value | If maintained well, equipment can be resold to recoup some of the initial investment. However, the resale market can be unpredictable, and prices might fluctuate. | There's no need to worry about resale as the asset isn't yours. |
Total Cost of Ownership vs. Total Cost of Renting | Beyond the purchase price, consider maintenance costs, storage, insurance, transportation fees (equipment to haul around your equipment), and potential finance charges. | Consider the rental fee, potential damage charges, and any other associated fees. |
Renting heavy equipment offers a flexible and cost-effective solution for many projects. Before committing to a rental, it's vital to understand the terms of the agreement, assess the actual costs, and ensure the machinery aligns with your project's needs. Whether you buy new, buy used, or rent, making an informed decision can significantly impact your project's success and your company's bottom line.